Thermal Adhesive: Difference between revisions
(Created page with "== Introduction == Thermal adhesive, also known as thermally conductive adhesive, is a type of adhesive specifically designed to conduct heat between components. This material is essential in various industries, including electronics, automotive, and aerospace, where efficient heat dissipation is crucial for the performance and longevity of devices and systems. == Composition == Thermal adhesives are typically composed of a polymer matrix filled with thermally conduct...") |
No edit summary |
||
Line 41: | Line 41: | ||
In electronic devices, thermal adhesives are used to bond heat sinks, spreaders, and other thermal management components to heat-generating parts like CPUs, GPUs, and power transistors. This ensures efficient heat transfer and prevents overheating. | In electronic devices, thermal adhesives are used to bond heat sinks, spreaders, and other thermal management components to heat-generating parts like CPUs, GPUs, and power transistors. This ensures efficient heat transfer and prevents overheating. | ||
[[Image:Detail-91847.jpg|thumb|center|Application of thermal adhesive on a CPU for heat dissipation.|class=only_on_mobile]] | |||
[[Image:Detail-91848.jpg|thumb|center|Application of thermal adhesive on a CPU for heat dissipation.|class=only_on_desktop]] | |||
=== Automotive === | === Automotive === |
Latest revision as of 09:21, 19 June 2024
Introduction
Thermal adhesive, also known as thermally conductive adhesive, is a type of adhesive specifically designed to conduct heat between components. This material is essential in various industries, including electronics, automotive, and aerospace, where efficient heat dissipation is crucial for the performance and longevity of devices and systems.
Composition
Thermal adhesives are typically composed of a polymer matrix filled with thermally conductive fillers. The polymer matrix can be made from epoxy, silicone, or polyurethane, while the fillers are often materials like aluminum oxide, boron nitride, or silver. The choice of polymer and filler significantly affects the adhesive's thermal conductivity, mechanical properties, and curing process.
Polymer Matrix
The polymer matrix serves as the base material that holds the thermally conductive fillers in place. Common polymers used include:
- **Epoxy**: Known for its strong adhesion and mechanical strength, epoxy-based thermal adhesives are widely used in electronic applications.
- **Silicone**: Silicone-based adhesives offer flexibility and high-temperature resistance, making them suitable for applications with thermal cycling.
- **Polyurethane**: These adhesives provide good mechanical properties and are often used in automotive applications.
Thermally Conductive Fillers
The fillers are responsible for the thermal conductivity of the adhesive. Common fillers include:
- **Aluminum Oxide (Al2O3)**: A cost-effective filler with moderate thermal conductivity.
- **Boron Nitride (BN)**: Offers high thermal conductivity and electrical insulation.
- **Silver (Ag)**: Provides excellent thermal conductivity but is more expensive.
Properties
Thermal adhesives possess several key properties that make them suitable for specific applications:
- **Thermal Conductivity**: The primary function of thermal adhesives is to conduct heat. This property is measured in watts per meter-kelvin (W/m·K).
- **Adhesion Strength**: The ability of the adhesive to bond surfaces together.
- **Curing Time**: The time required for the adhesive to harden and achieve its final properties.
- **Operating Temperature Range**: The range of temperatures within which the adhesive can function effectively.
- **Electrical Insulation**: Some thermal adhesives also provide electrical insulation, which is crucial in electronic applications.
Applications
Thermal adhesives are used in a variety of applications where efficient heat dissipation is essential:
Electronics
In electronic devices, thermal adhesives are used to bond heat sinks, spreaders, and other thermal management components to heat-generating parts like CPUs, GPUs, and power transistors. This ensures efficient heat transfer and prevents overheating.
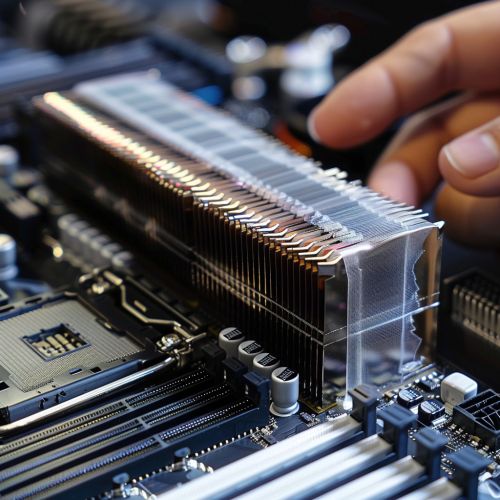
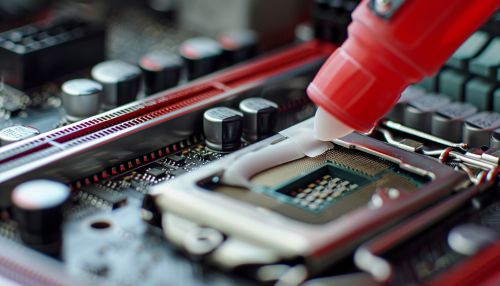
Automotive
In the automotive industry, thermal adhesives are used in battery packs, power electronics, and LED lighting systems. They help manage heat in high-power components, ensuring reliability and performance.
Aerospace
Thermal adhesives are critical in aerospace applications where components are subjected to extreme temperatures and thermal cycling. They are used in satellite systems, avionics, and other high-reliability applications.
Advantages and Disadvantages
Advantages
- **Efficient Heat Transfer**: Thermal adhesives provide a direct path for heat to flow from the heat source to the heat sink.
- **Mechanical Bonding**: They offer strong adhesion, which helps in maintaining the structural integrity of the assembly.
- **Electrical Insulation**: Many thermal adhesives also act as electrical insulators, protecting sensitive electronic components.
Disadvantages
- **Curing Time**: Some thermal adhesives require long curing times, which can be a drawback in high-volume manufacturing.
- **Cost**: High-performance thermal adhesives, especially those with silver fillers, can be expensive.
- **Application Complexity**: Proper application techniques are required to ensure optimal performance, which can add complexity to the manufacturing process.
Selection Criteria
Choosing the right thermal adhesive involves considering several factors:
- **Thermal Conductivity Requirements**: The required level of thermal conductivity depends on the specific application.
- **Operating Temperature Range**: The adhesive must be able to withstand the operating temperatures of the application.
- **Mechanical Properties**: The adhesive should provide sufficient mechanical strength and flexibility.
- **Curing Process**: The curing time and conditions should align with the manufacturing process.
- **Cost**: The cost of the adhesive should fit within the budget constraints of the project.
Future Developments
Research and development in the field of thermal adhesives are focused on improving thermal conductivity, reducing curing times, and enhancing mechanical properties. Advances in nanotechnology and material science are expected to lead to the development of new fillers and polymer matrices, offering better performance and cost-effectiveness.
See Also
- Heat Sink
- Thermal Interface Material
- Epoxy
- Silicone
- Polyurethane
- Boron Nitride
- Aluminum Oxide
- Silver